Use Case Overview
Robotics systems demand accurate and real-time position sensing to ensure precise movement, orientation tracking, and closed-loop control. In this application, the A33230 Hall Effect Sensor and the CT310 TMR Angle Sensor are evaluated as high-performance solutions for rotational position feedback in robotic joints and manipulators.
Through LiveBench, system engineers can remotely validate the behavior of these angle sensors in real-world robotics conditions, assess signal accuracy under magnetic interference, and fine-tune control systems—all without needing physical hardware onsite.
Application: Robotics Joint & Motion Control Systems
In modern robotics, precise motion control is a cornerstone of performance—whether in industrial automation, collaborative robots (cobots), or mobile robotics. Motors driving robot arms, end-effectors, and mobile joints require accurate feedback for angular position and rotational velocity to ensure repeatable, safe, and responsive movement.
Why Precision Angle Sensing Matters
Joint positioning systems rely heavily on closed-loop feedback to achieve smooth, accurate motion. Misalignment or drift in angular sensing can lead to poor accuracy, inconsistent operation, and even mechanical damage in multi-DOF (degrees of freedom) systems. Sensors like the CT310 (TMR) and A33230 (Hall-effect) enable real-time, high-resolution angular position monitoring.
How A33230 and CT310 Enable Precision in Angle Sensing for Robotics
- CT310 TMR Angle Sensor
Delivers ultra-low angle error and excellent linearity, ideal for detecting subtle changes in joint rotation even under stray magnetic fields. Its high accuracy makes it suitable for detecting fine-grain movement in robot wrists and grippers.
- A33230 Hall-Effect Sensor
Offers robust performance in harsh environments, supporting coarse positioning and providing redundancy in multi-sensor configurations. Its ease of integration and low latency supports fast control loops needed for dynamic motion systems.
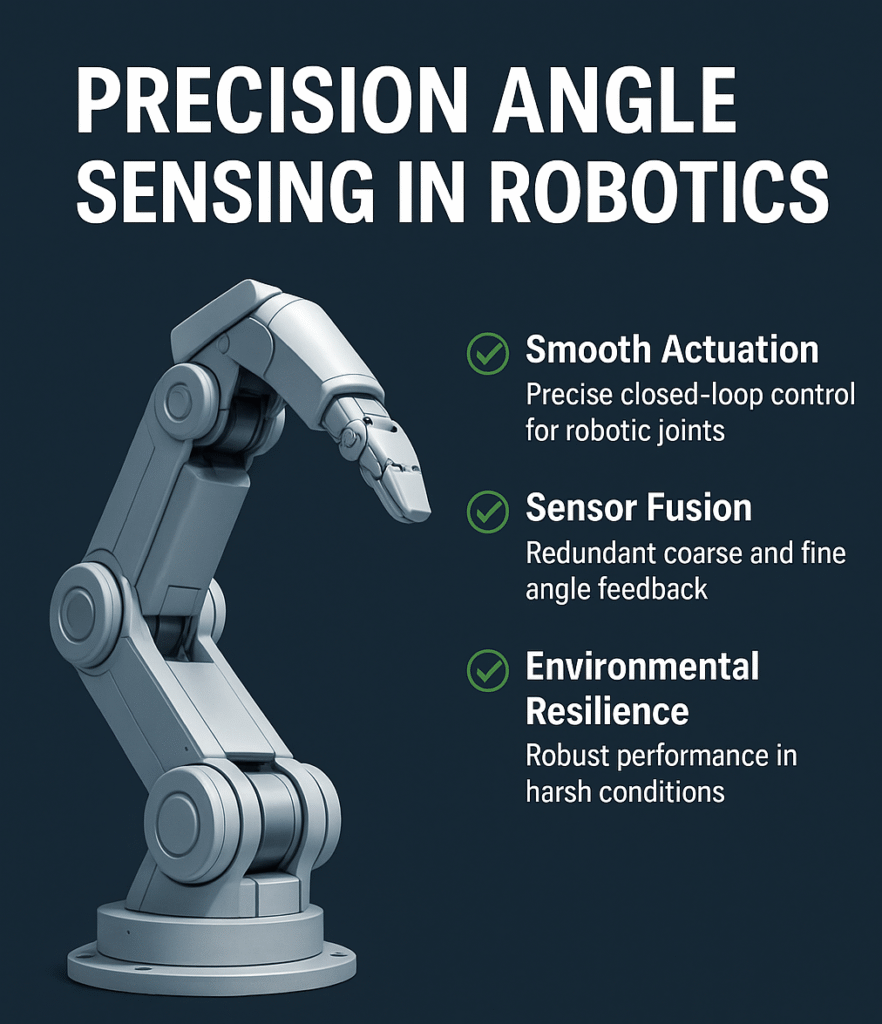
Use Case Benefits in Robotics
- Smooth Actuation: Enables precise closed-loop control for brushless DC (BLDC) or stepper motors, improving path-following and end-effector placement.
- Sensor Fusion: When used together, A33230 and CT310 can deliver layered feedback—coarse + fine—for high-stability positioning and fault detection.
- Environmental Resilience: Supports robotics deployed in noisy, high-EMI or temperature-sensitive environments (e.g., welding robots, warehouse AMRs).
Example Implementations
- Articulated robotic arms for assembly lines or surgical applications.
- Legged robots or exoskeletons requiring precise gait control.
- Automated guided vehicles (AGVs) using angle feedback for steering and docking systems.
Challenges Addressed
- Achieving accurate angular feedback in the presence of strong magnetic or electrical interference
- Ensuring real-time response in dynamic multi-axis robotic systems
- Maintaining signal integrity and resolution across a wide operating range
- Validating compatibility with low-power embedded control systems
LiveBench Evaluation Highlights
Real-Time Sensor Evaluation
- Instant access to live hardware via cloud-based testing
- Real-time monitoring of angle outputs in both sine/cosine and PWM formats
- Visual and waveform analysis of sensor signals under simulated rotation
Magnetic Immunity Assessment
- Evaluate stray field suppression of A33230 in high-EMI environments
- Compare field orientation sensitivity between Hall and TMR technologies
Dynamic Response Profiling
- Test response time and signal stability with motor-driven angular input
- Simulate robotic joint motion to observe live sensor feedback
System Integration Readiness
- Validate sensor outputs across typical supply voltages (3.3V, 5V)
- Measure output accuracy, linearity, and noise performance
- Check interfacing compatibility with microcontrollers and signal conditioning ICs.
Key Takeaways for Engineers
- Dual-sensor approach provides redundancy and flexibility in signal processing
- TMR sensors like CT310 offer superior sensitivity and linearity for high-precision robotic control
- Hall-based A33230 delivers robust stray field rejection ideal for industrial robot deployments
- Remote validation via LiveBench dramatically accelerates evaluation cycles from weeks to days
LiveBench Advantages
- No physical hardware required—evaluate instantly on real boards
- Live video feed for interactive hands-on observation
- Download logs and waveform data for deeper offline analysis
- Access application notes, datasheets, and detailed evaluation guides in one place