Introduction
A battery management system (BMS) is an electronic system designed to monitor, control, and optimize the performance of a battery pack, ensuring its safety, efficiency, and longevity. The BMS is an integral part of modern battery systems, particularly in applications such as electric vehicles, renewable energy storage, and consumer electronics. By managing battery performance and maintaining a safe operating area, the BMS helps prevent damage to the battery, reduces risks, and ensures consistent operation under varying conditions.
Definition of a Battery Management System
A battery management system (BMS) is a sophisticated control system that monitors and manages key parameters of a battery pack, such as battery status, cell voltage, state of charge (SOC), temperature, and charging cycle. The BMS ensures the battery operates within safe operating conditions, preventing issues such as overcharging, over discharging, or short circuits, which could lead to permanent damage or unsafe conditions.
Objectives of a Battery Management System
The main objectives of a BMS include:
Monitoring and Data Collection
The BMS continuously tracks parameters such as cell voltage, battery temperature, battery capacity, and current flow. This data is critical for evaluating the state of charge and ensuring optimal battery performance.
Ensuring Functional Safety
By identifying and mitigating unsafe operating conditions, the BMS ensures the safe operation of the battery pack and the connected device. It prevents overcharging, over discharging, and thermal runaway.
Cell Balancing
To maintain uniformity across individual cells, the BMS incorporates a cell balancing function. It ensures that all the cells in the pack operate at the same voltage and prevents over voltage in the most charged cells or undercharging in the less charged cells.
Thermal Management
The BMS regulates battery temperature using liquid cooling or air cooling to prevent overheating and ensure optimal performance.
Extending Battery Life
By managing charging current, charging cycle, and other operational factors, the BMS maximizes the battery life while maintaining efficiency.
Key Components of a Battery Management System
A BMS is composed of several essential components:
Cell Monitoring Unit
This unit measures the open circuit voltage and cell voltage of each individual cell, providing critical data for balancing and safety.Control Unit
The control unit processes data collected from the battery and ensures that the system operates within its safe operating area.Thermal Management System
A critical part of the BMS, this system uses air cooling or liquid cooling to maintain the temperature of the battery cells.External Communication Interface
The BMS communicates with other systems, such as the charger or vehicle control unit, using an external communication interface.Cell Balancing Module
The cell balancing function equalizes the voltage across all the cells to avoid over voltage or undercharging.Data Collection System
This component gathers secondary data, such as charge and discharge rates, total voltage, and battery level, which is used for further analysis and control.Safety Module
Ensures protection against short circuits, over charging, and over discharging, and prevents operation under stressful conditions.
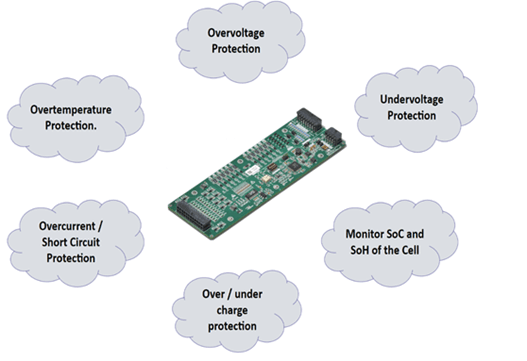
Fig 1 Key Functionalities of a Battery Management System (BMS)
Types of Battery Management Systems
There are two primary types of battery management systems based on their design and architecture:
Centralized BMS
Features a single control unit managing the entire battery pack.
Simplifies data collection and control but may face scalability challenges for larger systems.
Modular BMS
Employs a modular architecture where smaller BMS units manage groups of battery cells.
This system is more scalable and suitable for larger battery packs, such as those in electric vehicles.
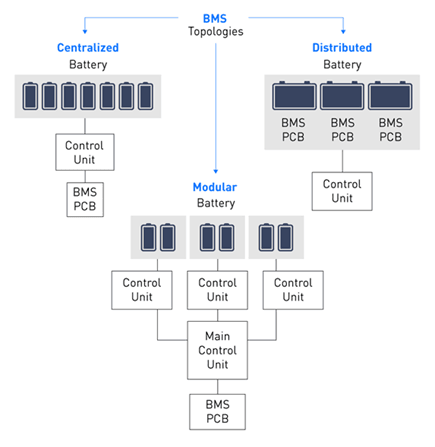
Fig 2 Types of Battery management System.
Best Practices for Battery Management
To ensure optimal battery performance and safety, the following best practices should be followed:
Prevent Overcharging and Over Discharging
Design the BMS to automatically prevent overcharging and over discharging of lithium ion batteries.
Overcharging can lead to thermal runaway, while over discharging can cause permanent damage to the battery.
Use Proper Thermal Management
Implement effective air cooling or liquid cooling to regulate battery temperature under high loads.
This minimizes heat-related wear and extends the battery’s lifespan.
Cell Balancing
Ensure the cell balancing function is active to equalize voltage across all the cells.
This helps maintain uniformity in the battery pack and avoids inefficiencies.
Incorporate Functional Safety Features
Integrate safety mechanisms to identify unsafe operating conditions and shut down the system when needed.
Optimize Charging Cycles
Design charging protocols that regulate charging current and charging cycle to improve battery life and efficiency.
Regular Monitoring and Data Analysis
Continuously monitor parameters like state of charge, cell voltage, and battery temperature to ensure a smooth operation.
Analyze secondary data to identify trends and potential issues early.
Applications of Battery Management Systems
Battery management systems are used in a wide range of applications, including:
Electric Vehicles
EVs rely heavily on a robust battery management system (BMS) to monitor lithium ion cells, manage energy, and ensure functional safety.
Energy Storage Systems
In renewable energy, battery systems are crucial for storing and distributing power efficiently. The BMS ensures the safe operation and optimal use of these systems.
Consumer Electronics
Devices like smartphones and laptops depend on BMS to optimize battery performance and protect against overcharging and overheating.
Industrial Applications
BMS is integral in industrial battery packages that power critical systems, ensuring consistent operation under stressful conditions.
Design Challenges in Battery Management Systems
Developing an effective BMS involves addressing several design challenges, including:
Thermal Management
Managing heat in lithium ion batteries is crucial to prevent thermal runaway and maintain performance.Scalability
Designing a BMS for large-scale battery packs with hundreds of cells requires a modular architecture to ensure reliability and scalability.Accuracy in Monitoring
Precise cell monitoring is essential to identify discrepancies in voltage, temperature, and SOC.Efficient Communication
Establishing reliable external communication between the BMS and other modules, such as chargers, can be challenging in complex systems.
The Future of Battery Management Systems
With advancements in technology, battery management systems are becoming more sophisticated, integrating features such as fast charging, passive balancing, and advanced data collection. Innovations in liquid cooling, control circuitry, and functional safety are enhancing the performance of lithium ion batteries in applications ranging from electric vehicles to renewable energy storage.
In the future, we can expect BMS designs to focus on:
Higher efficiency and reduced power losses.
Improved algorithms for state of charge estimation.
Enhanced scalability for larger battery systems.
Better integration with emerging technologies, such as IoT and AI.
Conclusion
A battery management system is a vital component in ensuring the safety, performance, and longevity of modern battery packs. By monitoring key parameters such as cell voltage, battery temperature, and state of charge, the BMS protects against overcharging, over discharging, and other potentially damaging conditions. Its applications span across industries, including electric vehicles, consumer electronics, and renewable energy storage.
As technology evolves, the role of BMS in optimizing battery life and performance will become even more critical, paving the way for safer and more efficient energy storage solutions. Whether in the form of modular architectures, enhanced thermal management, or smarter cell balancing functions, the future of battery management systems holds immense potential for innovation and progress.